陈树来,蔡玉俊,王玉广
(天津职业技术师范大学 机械工程学院,天津 300222)
摘要:本文开展超高强钢板热冲压模具冷却系统的优化设计研究。利用ANSYS/LS-DYNA模块对保压淬火过程零件及模具的温度场分布情况进行了数值模拟,分析均布水道的不足。在此基础上通过APDL(ANSYSParametric Design Language)参数化编程语言,选择零阶与一阶搜索相结合的优化算法,编写高强钢板热冲压模具冷却系统优化程序,得到优化的冷却水道位置。最后通过实验验证了优化结果的正确性。
关键字:高强钢板;热冲压;CAE分析;优化设计
近年来,随着人们环保意识的逐渐加强和对汽车安全性能要求的日益提高,各大汽车公司纷纷将重点放在汽车轻量化和安全性上。使用超高强钢板热冲压零件是减小汽车自重、加强汽车防撞性和抗冲击的最有效手段之一,具有巨大潜力。所以,超高强度热冲压技术已经成为世界各大汽车制造企业的热门技术。而热冲压工艺是将高强度钢板加热到奥氏体温度范围,钢板组织完成变化后,快速移动到模具,快速冲压,在压机保压状态下,通过模具中布置的冷却回路并保证一定的冷却速度,对零件进行淬火冷却,最后获得超高强度冲压件(组织为马氏体,抗拉强度在1500MPa甚至更高)的新型工艺[1-3]。正常情况下,在进行一系列的生产后,没有冷却系统的模具温度会达到200℃以上[4],但是只有模具的温度在200℃以下才能获得高强度的钢板。因此冷却系统的设计对板料最终所获得的机械性能和热冲压工艺的时间具有重大意义[5]。
本文在超高强度钢板热冲压成形保压淬火过程温度场数值模拟的基础上,利用APDL (ANSYSParametric Design Language) 参数化编程语言,选择零阶与一阶搜索相结合的优化算法,编写高强钢板热冲压模具冷却系统的优化程序,得到优化的冷却水道位置,并对优化结果进行了实验验证。
1 热冲压冷却系统的有限元模拟
1.1 建立有限元模型
本文的有限元模型包括两部分:板料和模具。板料的长、宽和厚度是200mm,100mm,2mm,圆角半径为5mm,冷却水道的初始位置是水道的中心距离模面是20mm,相邻管道之间的距离也是20mm。这里选取模具和板料整体的一个截面,又由于所选取的截面也具有对称性,则可以使用截面的1/4来建立模型(图1所示),这样既简化了建模,又减少了运算时间,降低了对硬件的要求。
图一 有限元模型
所选材料为热冲压专用钢板22MnB5,定义其物性参数,包括板料随温度变化的热传导系数、密度、比热容和模具的三个参数(表1所示)。根据相关理论研究的数据来定义热冲压零件的初始温度为810℃,热冲压模具的初始温度可以定义为与冷却水的初始温度相同为15℃[6]。热冲压过程中冷却速率至少是27℃/S[7]。
1.2 网格划分
网格是有限元分析的基本单元,直接关系到计算结果的正确性与准确性,在划分网格时,原则上网格越小,分析就越精确,但同时分析计算的时间也相应增加,对硬件的要求也要提高;如果网格过大,将会大大降低分析结果的准确性,甚至导致计算过程不收敛。本文所采用的单元类型为实体三角形六结点单元PLANE35,而根据模型的复杂程度(图2),应用智能网格划分在凸、凹模圆角处的网格设置的密一些,其他部位设置的稀疏一些(图3),这样既能满足分析精度也能减小计算时间和降低对硬件的要求。检查网格后,确认无网格缺陷。
1.3 边界条件确定
主要热量交换发生在模具和板料之间,水道和模具之间的对流系数h可以通过公式(1)进行计算得出:
A0——温度参数; ρ——水的密度,kg/m3; v——冷却水的流速,m/s; D——冷却管道的直径,m。所得出的冷却系数h 为30080W/(m2·K)
1.4 加载并求解
首先,选定分析类型为瞬态分析。根据分析并计算了的初始条件和公式(1)所得的对流系数等参数。温度施加在板料和模具有限元模型的结点上,而结点温度在整个瞬态分析过程保持不变,所以要先作稳态分析确定初始温度,并在第二步载荷步中删去刚才所设定的温度。
然后,设置载荷步选项,第一步的稳态分析设置时间0.01秒,时间步长为0.01秒,第二部之后的瞬态分析,国外发表相关文献设定的生产周期是30秒,零件在模具中20秒,剩下的10秒用于取出零件和放置下一个钢板,其中零件的淬火时间约是17秒,本文同样初步设定17秒,时间步长为0.1秒,为便于观测结果所有步长均为恒值。最后设置分析输出选项,存盘,进行求解。
1.5 模拟结果
在17秒的数值模拟之后,通过ANSYS /LS-DYNA 模块的专用后处理器LS-Prepost 得到模拟结果(如图4所示)为超高强度钢板在专用模具内保压淬火过程中的瞬态温度场分布图,图5为热冲压U型件在分析结束时的瞬态温度分布图。
从热冲压零件在模具内的瞬态温度分布图及零件的瞬态温度分布图可知,冲压件的最大温度为81.724℃,最低温度为43.191℃,热冲压零件在模具中保压淬火后温度分布不均匀,可以看出零件在弯角处的温度与其他部位的温度差较大,容易产生内应力,降低热冲压零件的性能。而产生这种结果的原因是由于冷却水道的尺寸和位置的不合理导致零件的降温效果不佳。所以我们以冷却水道的形状位置参数为设计变量,以零件冷却的平均温度为状态变量,以零件冷却的均匀程度为目标函数,对热冲压模具冷却系统进行了优化设计。
2 冷却系统优化设计
2.1 优化方法
使某个目的函数(即目标函数)在满足约束条件的同时达到最优值的传统方法有很多,本文所采用的优化方法:零阶法和一阶法。零阶方法最大的特点是只用到了因变量而没有用到因变量的偏导数。而一阶方法用到了设计变量的一阶偏导数,精度很高,尤其是在设计变量的变化范围较大,设计空间相对较大时。但是一阶方法可能在不合理的设计序列上收敛,对于这种情况,可以采用零阶方法。同时一阶方法也更容易获得局部最优值。但是如果起点附近有局部最优值,就会选择该最小值而找不到所要找的全局最小值。这时可以采用零阶方法或随机搜索的方法对一阶方法所得结果进行验证。
2.1.1 参数化建模
影响热冲压零件淬火过程温度场分布的结构是冷却水道的直径(或半径),冷却水道与模具成形面的距离和冷却水道之间的距离。而本文是基于参数化的优化设计,因此以水道与型腔之间的距离x、水道与水道之间的距离s、水道与临界空气的模具边之间的距离a、水道直径d作为优化设计变量(图6所示),以温度分布均匀作为优化目标。
2.1.2 状态变量的选取
状态变量就是优化分析中的约束条件,对于本论文的超高强度钢板热冲压模具冷却系统优化设计来说,当冷却水道的位置发生变化时,热冲压零件截面单元节点的温度平均值也随之发生变化,因而将热冲压零件截面单元节点的温度平均值作为状态变量。
2.1.3 优化目标函数的建立
优化过程中,正确目标函数的选择是最优化方法的核心,在保证单元网格划分足够细以保证计算精度的前提下,将热冲压模具中心截面处零件截面各单元节点的温度值对热冲压零件截面单元节点温度平均值的均方差来构成热冲压零件冷却的均匀性。所以,建立目标函数:如公式(2)。
其中,F— 目标函数;n— 热冲压零件截面单元节点个数;Ti— 热冲压零件截面单元节点的温度值;T — 所有热冲压零件截面单元结点温度值的平均值;a— 比例因数,衡量热冲压零件温度平均值T 和热冲压零件平均温度的均方差
的相互作用,数值在(0,1)内变化,本文取a =0.581。
2.1.4 优化步骤
(1)进入通用后处理模块(POST1),从瞬态分析结果中提取热冲压零件截面所有节点温度的平均值,再根据各结点温度值与温度平均值计算出目标函数值来。并赋值给相应的变量参数。
(2)优化文件必须包括整个分析过程且应尽量的简练,只有交互过程中需要看到显示(如EPLOOT等)时或将其定位到一个显示文件(/SHOW)中时可以包括在分析文件中。
(3)进入优化分析模块,指定分析文件、设计变量及其变化范围和公差、状态变量及其变化范围和公差,还有目标函数及其公差,指定优化分析策略,由于本文主要研究超高强度钢板热冲压模具冷却系统的设计,则首先采用随机搜索方法得出一系列的初始设计序列,去除其中不合理的设计序列,然后在此基础上采用零阶方法进行优化分析,最后得出最优设计序列。
(4)优化迭代结束后,设计变量与目标函数间的变化关系可以通过图形表示出来。在默认情况下,在名为Jobname.RFL 的文件中保存着最后的设计方案的模拟结果。要获得初始设计结果,应该在初始分析完成后,进入后处理器查看并保存及输出数据。
3 优化结果与分析
表2为初始设计序列与优化序列分别代表的冷却系统参数序列,在此说明一下,本论文得到的最优设计并不是理想的绝对最优解,是因为在设计初我们做了近似的假设;优化分析所得解的精确程度与最大迭代次数、目标函数工程等因素有关。
接下来对优化后的分析结果进行模拟仿真,数值模拟的时间仍是在17秒,而通过优化设计后,从图7、8所示可以看出,热冲压零件的最高温度为45.359℃,最低温度为36.939℃,热冲压零件的冷却效果有了较明显的改善,特别是零件弯曲部位淬火冷却的均匀性有了很大的提高。图8与图5对比可知,零件的温度最高值降低了36.325℃,又说明了冷却系统的优化设计对热冲压零件的冷却效果有了明显的改善。
4 实验验证
4.1 实验装置及过程
本文选用自行设计的热冲压模具(图9、10所示)。选用功率为30kW的箱式电阻炉(炉膛尺寸350mmx300mmxl50mm)对钢板进行加热,用火钳将加热后的钢板快速移动到冷却系统进行优化后的模具中,选用Y32-100压力机对零件进行保压淬火,而由于超高强度钢板热冲压是从850℃到900℃降至200℃以下,所以初选测量零件温度变化过程的传感器为K型热电偶温度传感器,其测量温度范围为:0℃至1200℃。
4.2实验结果与分析
由于冷却水道的存在给测量增加了难度,导致安置传感器的位置受到限制,不能将U形件中的所有点温度都测量出来,因此本次实验对超高强度钢板热冲压成形过程中的四个位置进行测量,测量到图11中四个点随时间变化的曲线(图12所示),其中曲线01到04分别代表D1至D4 四个点的温度变化曲线。
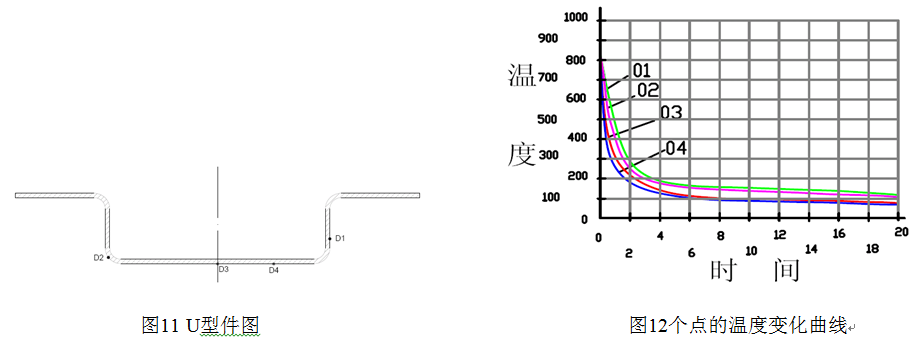
通过对U形件进行超高强度钢板热冲压成形试验及对成形件的测量,可以看出,所设计并优化后的冷却系统基本上达到了预期的效果,虽然四个点的温度都比数值模拟的高些且有一定的差别。但是实际温度比模拟的高是由于实际零件与模具间的传热是有热阻的,四个点的温度有差别也是因为零件侧壁与凹模的接触不完全,所以温度比较高,而零件弯角处的温度相对较低是因为与凸模的接触较好传热较快所致的。总体说来,零件的温度分布比较均匀,证明了优化结果的正确性。而虽然试验选的是形状简单薄厚均匀的U形件,但是对于形状复杂薄厚不均的零件其模具冷却系统的设计及优化方法是一样或相似的。
5 结论
本文开展了高强钢板热冲压保压淬火的有限元分析及冷却水道的优化设计研究。结论如下:
(1) 热冲压模具中均匀分布的冷却水道会导致成形件温度分布的不均匀,影响零件的机械性能,因此需要对热冲压模具的冷却水道开展优化设计。
(2) 有限元模拟及实验验证表明:运用APDL(ANSYS Parametric Design Language)的参数化编程语言,结合零阶与一阶搜索优化算法可以实现高强钢板热冲压模具冷却系统的优化设计,为高强钢板热冲压模具的设计提供理论基础。
参考文献
[1] 康斌.国内外高强度汽车板热冲压技术研究现状[J].冶金管理,2009,8:58-60.
[2] 胡平,马宁,郭威,等.超高强度汽车结构件热冲压技术研究进展[C].上海,2010 力学与工程应用学术研讨会论文集.
[3] 林建平,孙国华,朱巧红,等.超高强度钢板热成形板料温度的解析模型研究[J].锻压技术.2009,34(1):20-23.
[4] Sikora,S.,Lenze,F.-J.,Hot-Forming Important Parameters for the Production of High-Strength BIW Parts[C]. IDDRG,
2006:295-301.
[5] H.Hoffmann, H. So, H. Steinbeiss, Design of Hot Stamping Tools with Cooling System[C].Germany: Elsevier,Annals ofthe
CIRP,2007:269-272.
[6] A.Shapiro, Using LS-DYNA to Model Hot Stamping[C]. USA:Livermore Software Technology Corporation,2009:37-
45.
[7] Merklein, M., Lechler, J., Geiger, M., Characterisation of the Flow Properties of the Quenchenable Ultra High