|
|
管子卡箍复杂零件多工位级进模设计 |
2013/4/2 |
金龙建
宝烁模具(上海)有限公司(上海 201323)
摘要:文中分析了管子卡箍的冲压工艺,介绍了其级进模总体结构及排样方案。说明了模具结构的特点,该模具上下模板具有高精度和长寿命,可快速更换凸模及下模镶块,重复装配精度高。经多年来生产验证,该模具结构合理、可靠、送料稳定,并能保证零件的质量,对此类似的零件设计具有参考价值。
关键词:管子卡箍;冲压工艺;排样图;级进模;模具结构。
1 引言
图1为国外某汽车管子通用卡箍件。材料为ST14,板料厚度为1.2mm,年产量为50多万件。其形状及尺寸详见图1所示,该零件旧工艺采用单工序模来生产,所需模具多,冲床利用率及生产效率低,且工序间手工放置半成品有误差,导致零件质量不稳定。这样既增加了冲压的人工成本和制件废品率,又降低了机床利用率,且机床投资成本也较大。
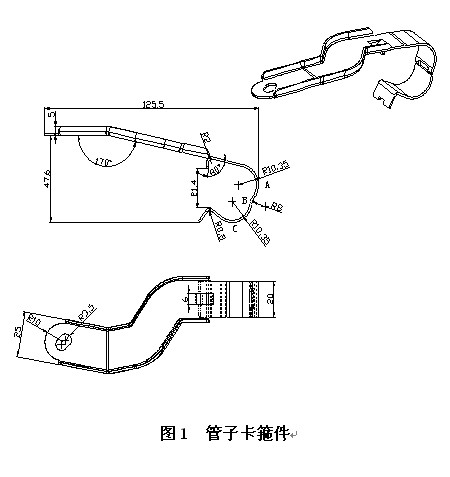
随着产量的日益增长,为适应大批量生产及保证零件的质量,将单工序模设计成自动送料的多工位级进模。在解决上述问题的同时还可确保生产的安全性,降低工人的劳动强度和生产成本。有效保证了零件的质量,提高该零件在市场的竞争能力。
2 工艺分析
该零件形状复杂,尺寸精度要求高,在生产中需经过冲裁、切舌、多次弯曲及翻边等多道工序完成。计算出弯曲展开长度为183.6mm (零件展开如图2所示)。从图1零件图可以看出,该零件头部弯曲工艺比较复杂。头部弯曲部分有2个R10.35mm、1个R8mm和1个R0.8mm等组合而成。从零件的结构分析,该零件的关键部位为头部2个R10.35mm和1个R8mm组合尺寸回弹较大,导致零件的质量不稳定。为克服此回弹,经分析,该零件头部需经过4次弯曲成形,具体详见图3排样图A-A、B-B、C-C、F-F所示。其弯曲数量无论多少,均可经合理分解后,按一定的成形顺序要求设置在不同的冲压工位上。
在连续生产中,而带料进行不断的连续冲压。送进过程中冲压件与载体间的连接强度也不断的降低。带料的导料方式和每步工序定距形式是否合理采用,对冲压件在生产中的稳定性非常重要,在排样设计时应充分考虑这一点。
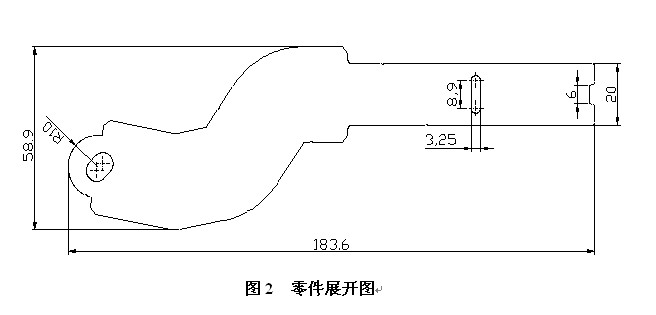
3 排样设计
众所周知,在级进模设计中,排样设计是级进模的关键环节。是否能达到冲压件设计要求的重要一步。它不但从材料的利用率、零件质量、生产效率和模具寿命等多方面考虑,决定零件成形过程中的工位数、不同工序先后次序、步距大小和定位方式等。还应考虑零件的精度,冲压成形规律及模具强度等问题。
该零件排样设计时主要考虑以下9个方面:
(1)采用模具刚性好、精度高的级进模通用模架;
(2)合理制定工位数,以适应模架周界及考虑累积误差对零件精度的影响;
(3)复杂的型孔应分解为若干个简单的孔形,并分成几个工步进行冲裁,使模具制造简单,但同一尺寸或位置精度要求高的部位应尽量在同一工位上冲出;
(4)合理制定步距,以适应凹模强度及弯曲成形的位置;
(5)由于零件有冲裁、多次弯曲及翻边等工序,各工序的先后应按复杂程度而定,以有利于下道工序的进行为准,并应先易后难,先冲平面形状后冲复杂形状,而弯曲成形部位相关联的必须先冲切出;
(6)排样时必须合理安排导正销孔的位置,以适应零件精度要求;
(7)需要冲制的零件与载体的连接应具有足够的强度和刚度,以保证条料在冲压过程中连续送进的稳定性;
(8)尽可能使级进模的压力中心与压力机的压力中心一致;
(9)尽可能提高材料的利用率以节约成本,该零件采用20°斜排排列方式。
根据上述分析,该零件共有21个工步,即工步1为冲导正销孔及冲切侧刃;工步2为冲切外形废料;工步3为冲切外形废料及冲切腰形孔;工步4为冲切外形废料及冲切腰形孔;工步5为冲切外形废料;工步6为空工位;工步7为首次弯曲成形;工步8为二次弯曲成形;工步9为空工位;工步10为三次弯曲成形;工步11为切舌;工步12为80°弯曲成形;工步13为四次弯曲成形;工步14为空工位;工步15、16为冲切外形废料;工步17为空工位;工步18为翻边;工步19为空工位;工步20为弯曲成形;工步21为冲切载体(载体与零件分离)。计算出条料宽度 196mm,步距45mm ,通过导正销与侧刃为条料的精确定距。
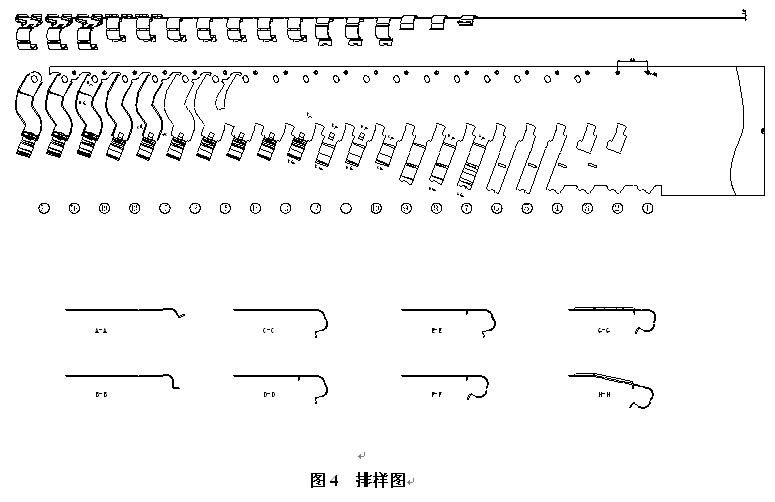
4 模具结构特点
如图5所示为模具结构图。该模具结构紧凑,设计巧妙,为确保上下模对准精度。该模架采用4个精密的滚珠钢球外导柱。而模板内各设计了12个精密的内导柱。这样一来大大增加模具的使用寿命。其结构设计如下:
(1) 采用滚动式自动送料机构传送各工位之间的冲裁及成形工作,用导料板导料、顶杆及顶块抬料。
(2) 凸模固定板、卸料板和下模板之间另采用滑动小导柱进行导向,小导柱和小导套采用标准件。有了小导柱,不但进一步提高了模具的导向精度,同时也方便模具的装配。
(3) 为保证精度,凸模,凹模等各零件采用SKDII (其热处理硬度为HRC60 ~62 HRC);所有模板材料均采用Cr12MoV,其硬度值根据各板功能不同有所区别。固定板垫板、下模板垫板硬度为56~58HRC,特别是固定板垫板必须达到要求,因为固定板垫板承受凸模的压力,下模板垫板承受凹模镶块的压力,如硬度不高,凸模或凹模镶块将在垫板上压出塌陷,从而影响模具精度。下模板、卸料板硬度为54~58HRC,卸料板垫板和凸模固定板硬度为56~60HRC。因为弯曲成形的弯曲凸模在凹模板和卸料板内滑动,如板和弯曲凸模硬度一致则很容易咬死,所以将下模板和卸料板硬度做低一点。
(4) 冲裁凹模和弯曲凹模设计成镶块镶入下模板内,刃磨刀口及调整弯曲回弹时只磨镶块即可,然后用垫片将凹模镶块与下模板垫平,这样可大大提高模具寿命。
(5)卸料板采用弹压卸料,由于卸料板还担当凸模的导向,为了保证卸料板与其他模板的平行度,卸料板的连接采用卸料螺钉组件5、16,套管用夹具在磨床上一次磨出两端面,所有的套管高度一致,从而保证卸料板与其他板的平行度≤0.01mm,也保证了凸模和凹模间的相对位置准确。
(6)出件和排料设计。该模具中冲裁的废料包括最后工位切除载体废料均从凹模孔通过下模座排出。最后工位的制件利用切断凹模将已成形好的零件从载体上切断,使分离后的制件靠自身的重量从另一侧下模型腔内滑下。
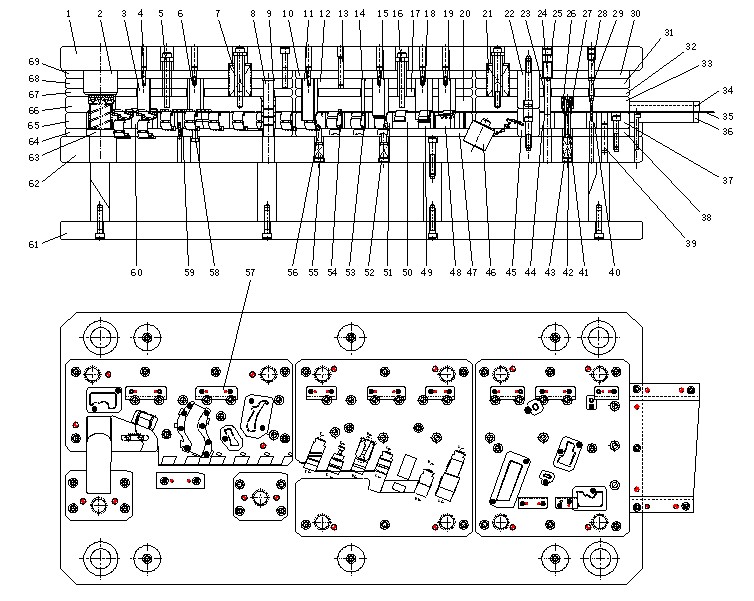
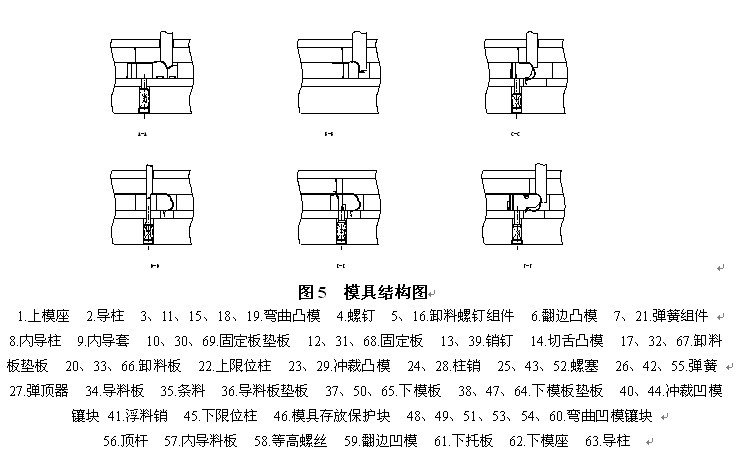
5 模具零部件结构设计
5.1 防倾侧结构设计
从排样图可以看出,带料的部分边缘是单边冲切。那么凹模刃口的冲裁间隙是放冲裁这一面,而另外一面间隙是零配零的,当凸模进入凹模冲裁时造成单边受力,力的方向全部集中在外侧的一边,而凸模在脱料板的间隙下倾斜在外侧的一边。造成凸模外边的一面刃口与凹模的刃口发生微小的相碰撞,影响零件的冲切精度。所以该凸模采用防倾侧结构,可以解决上述的问题,使模具在生产中更稳定。结构是:当模具往下冲压时,凸模的靠刀部位2先导入下模镶件5,再进行冲切(见图6所示)。
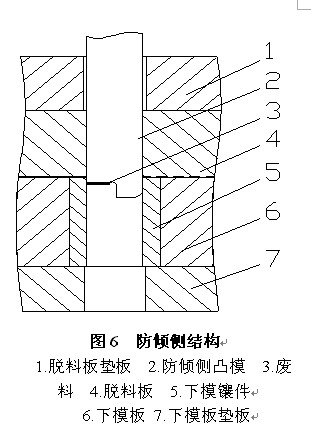
5.2 快速更换凸模
该模具除个别凸模较单薄进行阶梯式补强并用挂台进行固定,如图5模具结构序号14所示,其余统一用螺钉固定(见图7所示)。在凸模后面攻有螺纹孔,即在固定板和上模座的对应位置分别钻螺钉过孔及螺钉头部通孔,螺钉从上模座穿过固定垫板与凸模连接。当凸模需经更换和修磨时,把凸模固定螺钉拆掉并用销钉从凸模固定板中顶出即可。不必松动连接固定板与上模座的螺钉和销钉,也不必拆掉脱料板,这样更换凸模速度快,而且不会影响固定板的装配精度,从而保证模具重复装配精度,延长模具的使用寿命。
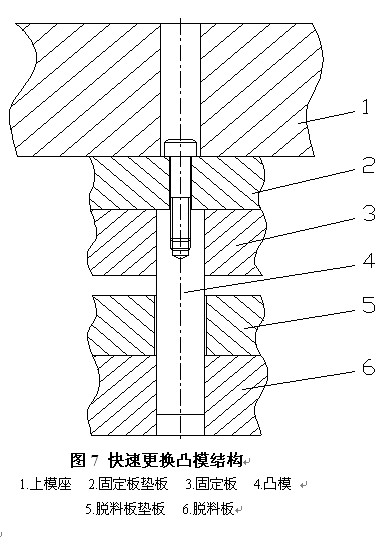
5.3 快速更换凹模镶块
此零件需求量庞大,其凹模镶块(冲裁刃口)容易损坏,需经常更换。该级进模按图8所示设计了凹模镶块。该下模镶块外侧不带台阶用螺钉固定。在凹模镶块钻有M6的螺钉通孔及沉头孔,并在M6的螺钉通孔内攻有M8的螺纹。
如更换或修模时,拆卸M6螺钉2,用M8螺钉拧入凹模镶块M6的螺钉通孔内攻有M8的螺纹里,并用手拉动M8螺钉即可取出凹模镶块3,不必拆卸联接下模板的螺钉及销钉,有时还无需将模具从冲床上卸下,因此更换凹模速度快,而且可保证模具的重复装配精度,提高模具的使用寿命。
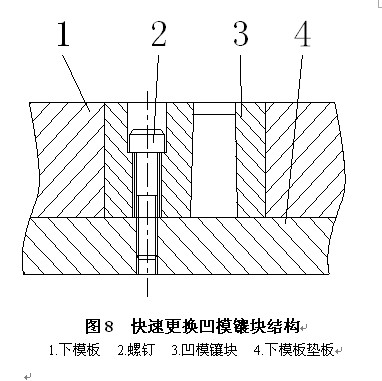
结束语:
在当今世界上,高度发达的制造业和先进的制造技术已成为衡量一个国家综合经济实力和科技水平的最重要标志之一,其中汽车零配件的数量也随着日益增大。追求产品价格及质量十分剧烈,采用先进的级进模技术是一项行之有效的最佳途径。该零件形状较为复杂,在生产中需经过冲裁、弯曲、成形等多工序,可在一副级进模上冲制完成。它既能减小设备投资,又可提高产品尺寸精度及生产效率,同时还可以确保工人生产的安全性,从而大大减轻劳动力及降低了产品成本,经济效益十分显著。
参考文献:
[1] 洪慎章,金龙建. 多工位级进模设计实用技术[M]. 机械工业出版社,2010(8).146~155
[2] 陈炎嗣. 多工位级进模设计手册[M]. 化学工业出版社,2012.1
[3] 金龙建.多工位级进模典型结构图册[M]. 化学工业出版社,2012.2
[4] 金龙建. 窗帘支架弹片多工位级进模设计[J]. 模具工业,2010(4):34 ~37
[5] 金龙建. 支架自动攻丝级进模设计[J]. 模具工业,2011(7):15 ~ 18
[6] 金龙建. 连接支架自动攻丝多工位级进模设计[J].模具制造,2011(12):84 ~87
作者简介:金龙建 (1979年11月—),男,浙江省临海市东塍人,工程师。主要从事冲压工艺及模具设计工作;地址:上海市南汇区祝桥镇金顺路16号,宝烁模具(上海)有限公司。电话:13564253153 E-mail:jinlongjian2010@163.com |
|
|
|
|