A侧管连续拉深模设计
金龙建
(宝烁模具(上海)有限公司,上海 201323)
摘 要:文中通过对A侧管的工艺分析及计算,提出了落料、冲孔、拉深成形工艺,介绍了连续拉深模的冲压方案。经多年来生产及验证,该模具结构清晰、可靠、加工质量好,生产效率高,对此类零件的级进模设计有重要的参考价值。
关键词:A侧管;冲压工艺;排样设计;级进模;模具结构。
中图分类号: 文献标识码: 文章编号:
0 引言
该制件为某家用电器的部件之一,材料为SUS304不锈钢,板料厚度t=0.2mm,年需求量较大(年产量900多万件)。该制件外形由内径ø13.6±0.02mm、ø16.6±0.02mm和凸缘ø19±0.02mm的尺寸组成,高度由18.4±0.03mm和19.3±0.03mm的尺寸组成,底部由一个六角形异形孔和四个小凸点组合,从制件的直径和高度的公差分析,设计一副高精度的连续拉深模冲压才能达成。
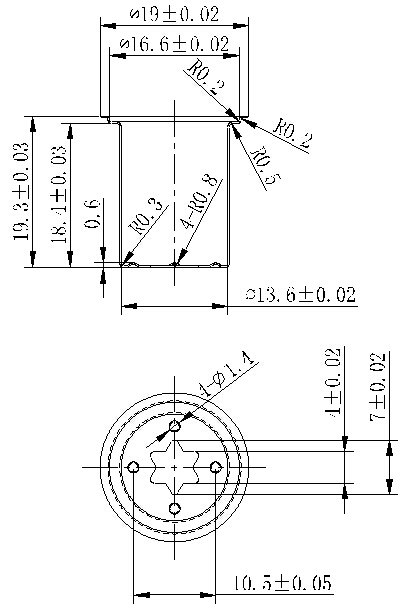
图1 A侧管
1 工艺分析及计算
1.1 工艺分析
从图1可以看出,该制件是一个狭边凸缘圆筒阶梯拉深件,形状复杂,尺寸要求高。其冲压工艺有工艺切口、冲孔、拉深及落料等工序组合而成,特别工件在拉深成形时,既要保证料带平直不变形,又要减少拉深的阻力,使材料容易流动成形,冲压后获得较高的产品质量。该制件的毛坯在带料上采用了双圈圆形三面切口的搭边方式,并在带料两侧,两个工位之间的余料处设有两个ø4.0mm的导正销孔(见图2所示),以保证带料的送料精度。因制件材料较薄,为了使送料更稳定,该模具采用拉料机构来传递各工位之间的冲压工作。
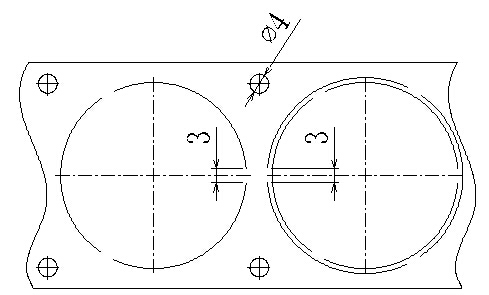
图2 双圈圆形三面切口的搭边图
1.2 拉深工艺的计算
1. 毛坯计算
从实际经验及制件的技术要求把修边余量调整为δ=1.8mm,得凸缘直径:
图3 坯料尺寸计算图
2. 拉深系数及各次拉深直径计算
拉深系数是一个重要的工艺参数。此制件首次拉深把凸缘边上的小阶梯部分的材料全部拉入凹模内,因此首次拉深按无凸缘零件计算拉深系数,由毛坯相对厚度得:
t/D×100=0.2×100/39.5=0.506≈0.51
从资料查得首次拉深m1=0.55~0.58,那么以后各次拉深mn取0.83~0.88。首次拉深材料还没硬化,塑性好,那么拉深系数可取小些。由于不锈钢零件再拉深的硬化指数相对较高,而塑性愈来愈低,变形越来越困难,故拉深系数一道比一道大,在工步2、3次拉深设计有定位套装置,使零件在成形过程中均匀变形,那么拉深系数可略取小些。
根据经验值调整后的拉深系数为:m1=0.57,m2=0.82,m3=0.87,m4=0.88,m5=0.9。所得各次拉深直径为:
从上式计算可以看出的直径同图1 A侧管的外径基本相等,那么该制件为四次拉深即可。
3 排样设计
排样设计是级进模的关键环节。也是级进模设计的前提和基础,它具体反映了制件在整个冲裁、拉深成形过程中的工位位置和各工序拉深次数、拉深高度及拉深直径大小的相互关系。
经分析,该制件采用单排排样较为合理,因制件坯料直径为ø39.5mm,根据经验值得,n1=3.4mm, n2=1.05mm, b2=2.7mm,求得料带宽度计算如下:
B=dj+2n2+2b2
=39.5+2×1.05+2×2.7
=47mm;
式中:B——料带宽度
dj——首次拉深展开直径
n2——制件搭边
b2——侧搭边宽度
料带送进步距计算如下:
p=dj+n1+2n2
=39.5+3.4+2×1.05
=45mm
式中:p——料带送进步距
dj——首次拉深展开直径
n1——切口搭边,
n2——制件搭边
从上式计算得知,该制件料带宽度为47mm,,料带送进步距为45mm,该排样共设计成17个工位(如图4所示),即工位①:冲导正销孔及内圈切口;工位②:空工位;工位③:外圈切口;工位④:空工位;工位⑤:首次拉深;工位⑥:空工位;工位⑦:二次拉深;工位⑧:三次拉深;工位⑨:四次拉深;工位⑩:底部压凸;工位11:阶梯拉深;工位12:空工位;工位13:冲底孔;工位14:空工位;工位15:整形;工位16:空工位;工位17:落料。
图4 排样图
4 模具结构与冲压动作
如图5所示为A侧管模具结构图,该制件年产量较大,为确保各工序拉深凹模及落料刃口的使用寿命和稳定性,各工位的拉深凹模及落料刃口采用硬质合金(YG15)镶拼而成。该模具结构较为复杂,有拉深、阶梯拉深、冲底孔等,为使各工序调整及维修更方便,该模具由多组模板组合而成的精密连续拉深多工位级进模,具体模板分组如下(见图5所示):
①上垫板、固定板垫板及固定板分别由3组模板组合而成;
②卸料板垫板及卸料板分别由9组模板组合而成;
③下模板及下模板垫板分别由4组模板组合而成。
上模部分和下模部分的各组模板分别安装在整体的上模座及下模座上,并用4套ø38mm的精密滚珠导柱及20套内导柱作为精密导向件。
图5 模具结构
1.上模座 2. 内圈切口滑动块 3. 内圈切口凸模 4. 内圈切口凸模固定块 5. 外圈切口滑动块 6. 外圈切口凸模固定块 7. 外圈切口凸模 8. 卸料板垫板-2 9. 首次拉深压边圈 10. 首次拉深凸模 11. 卸料板-2 12. 卸料板垫板-3 13. 上垫板-2 14. 卸料板-3 15. 定位套-1 16. 二次拉深凸模 17. 顶针-1 18. 定位套-2 19. 三次拉深凸模 20. 顶针-2 21. 固定板-2 22. 卸料板垫板-4 23. 四次拉深凸模 24. 卸料板-4 25. 压凸点凸、凹模 26. 卸料板垫板-5 27. 卸料板-5 28. 口部拉深凸模固定块 29. 口部拉深凸模 30. 固定板垫板-2 31. 卸料板-6 32. 卸料板垫板-6 33. 冲底孔凸模固定块 34. 冲底孔凸模 35. 卸料板垫板-7 36. 卸料板-7 37. 整形凸模 38. 内限位销 39.卸料板垫板-8 40.卸料板-8 41. 落料凸模 42. 落料凸模固定块 43. 上垫板-3 44. 固定板垫板-3 45. 固定板-3 46. 卸料板垫板-9 47. 落料滑动块 48. 卸料板-9 49. 下模板-4 50. 下模板垫板-4 51. 下模座 52. 下垫脚-3 53. 落料凹模 54. 落料凹模垫块 55. 弹簧底板-2 56. 下模板垫板-3 57. 整形凹模 58. 等高套筒 59. 整形滑动块 60. 下模板-3 61. 工件导向块 62. 冲底孔凹模固定块 63. 冲底孔凹模垫块 64. 冲底孔凹模 65. 冲底孔滑动块 66. 下模板垫板 67. 口部拉深凹模 68. 口部拉深滑动块 69. 凸点成形顶杆 70. 垫圈 71. 压凸点凹模 72. 四次拉深凹模 73. 四次拉深顶杆 74. 四次拉深滑动块 75. 三次拉深顶杆 76. 三次拉深凹模77. 二次拉深顶杆 78. 下垫脚-4 79. 二次拉深凹模 80.下模板-2 81. 套式顶料杆-3 82. 弹簧底板-1 83. 首次拉深顶杆 84. 首次拉深凹模 85. 外圈切口顶块 86. 套式顶料杆-2 87. 外圈切口凹模 88. 套式顶料杆-1 89. 内圈切口顶块 90. 下垫脚-1 91. 内圈切口凹模 92.下模板垫板-1 93.下模板-1 94. 承料板 95. 卸料板-1 96. 卸料板垫板-1 97. 固定板-1 98. 固定板垫板-1 99.上垫板-1 100. 导料板-1 101.导料板-2 102.导向顶杆-1 103. 导向顶杆-2 104.下垫脚-2 105. 导向顶杆-3 106.限位柱 107. 下垫脚-5
4.1 定位套设计
为保证拉深件得到较好的定位,该模具除带料两侧两个工位之间的余料处设有ø4.0mm的导正销正确定位之外,还在二次拉深及三次拉深的凸模上设有两个不同大小的定位套(具体见图6所示),使板料成形时塑性变形较均匀。此结构在连续模中设计较复杂,制作精度要求也较高。
结构是:当模具从上极点往下冲压时,首先定位套3完全定好前一工位送过来的拉深件内径,再继续往下冲压时,拉深凸模1进入拉深凹模7进行拉深成形。
图6 定位套结构
1.拉深凸模 2.顶针 3.定位套 4.卸料板垫板 5.卸料板
6.下模板 7.拉深凹模 8.顶杆 9.反推杆
4.2 空工位设计
该模具在工位②、工位④、工位⑥、工位12、工位14及工位16各留一个空工位,其中工位②和工位④的空工位是为了内、外圈切口后校平作用;在工位⑥安排一个空工位,然后后序拉深成形时,由于不同的拉深高度导致载体的送料面与模面的表面不平行,即拉深的轴心线和模具表面产生一定的斜角,这对后序拉深对制件的质量有影响,为保证制件的质量,以空工位来保证带料的工作长度,以此减小料带的倾斜角;由于该制件拉深次数多,在工位12留一个空工位,必要时可作为后备拉深工序;为了减少拉深工序同冲底孔工序之间的断差,在工位14及工位16各留一个空工位以此减小料带的倾斜角。
4.3 模具冲压动作
将原材料宽47mm,料厚t=0.2mm的卷料吊装在料架上,通过整平机将送进的带料整平后,开始用手工将带料送至模具的导料板,进入第一组的导向顶杆,直到进入工位①同工位②之间的余料处为止,这时进行第一次内圈切口;第二次为校平;依次进入第三次内圈切口;第四次为校平;进入第五次首次拉深;第六次为空工位;进入第七次为二次拉深;进入第八次为三次拉深;进入第九次为四次拉深;进入第十次底部压小凸点;进入第十一次阶梯拉深;第十二次为空工位;进入第十三次为冲底孔;第十四次为空工位;为保证制件的质量,进入第十五次整形工序;第十六次为空工位;这时整个制件拉深成形已全部结束,最后(第十七次)将载体与制件分离,再连续用手工送至冲压出三个制件,利用制件同载体分离后,留在载体上的圆环形余料进入拉料器的拉料钩内(注:拉料器机构没有在图中体现出来),即可进行自动连续冲压。
结束语:
该模具结构巧妙、设计合理,通过对制件的工艺分析,该带料在排样时毛坯在带料上采用了双圈圆形三面切口的搭边方式,既保证料带平直不变形,又要减少拉深的阻力,使材料容易流动成形,获得较高的产品质量,经过四年来的生产验证,满足了大批量生产的要求。
参考文献:
[1] 洪慎章,金龙建. 多工位级进模设计实用技术[M]. 机械工业出版社,2010.(8):
[2] 陈炎嗣. 多工位级进模设计手册[M]. 北京:化学工业出版社,2012.(1):750~755
[3] 金龙建. 多工位级进模典型结构图册[M]. 化学工业出版社,2012.(2):247 ~ 249
[4] 金龙建. 阶梯圆筒形件级进模设计[J],模具工业,2010 (2):14~17
[5] 金龙建,金龙周. 阶梯拉伸件多工位级进模[J]. 模具制造,2011(4):16 ~ 19
作者简介:金龙建 (1979—),男,浙江省临海市东塍人,工程师。主要从事冲压工艺研究及模具设计工作;地址:上海市南汇区祝桥镇金顺路16号,宝烁模具(上海)有限公司。(电话)13564253153 (电子信箱)jinlongjian2010@163.com